

Markandeya, S., Merchant, D., Sha, D., et al. Melamed Y, Kiselev A, Gelfgat M et al (1996) Hydraulic hammer drilling technology: developments and capabilities. Petroleum Drilling Techniques 41(06):40–43
/is2.ecplaza.com/ecplaza2/products/7/73/736/1392346743/4587510.jpg)
Lei P, Ni HJ, Wang RH et al (2013) Field test of self-excited vibration rotary percussion drilling tool in deep and ultra-deep wells. Li GH, Bao HZ, Tao XH (2004) Effects of drilling conditions on crushing rocks while rotary percussion drilling. Lin YH, Shi TH, Li RF et al (2005) Simulation of impact force and penetration rate of air hammer bit drilling. Lin YH, Shi TH, Liang Z et al (2004) Simulation of penetration rate of air percussion drilling bit. (1993) “Wear and damage to PDC bits.” SPE 2629 Kaitkay P, Lei S (2005) Experimental study of rock cutting under external hydrostatic pressure. Karasawa H, Misawa S (1992) Laboratory testing to design PDC bits for geothermal well drilling. Petroleum Drilling Techniques 34(01):13–16 Jiang HW, Liu YS, Zhai YH et al (2006) Research on rock crushing mechanics model in rotary and percussive drilling. Howard GC, Vincent RP, Wilder LB (1960) Development and field use of a high-frequency gas-operated rotary-percussion drilling tool. (2005b) “Dynamically modelling rock failure in percussion drilling.” The 40th US Symposium on Rock Mechanics (USRMS). (2005a) “Percussion drilling in oil industry: review and rock failure modelling.” The AADE national technical conference and exhibition, pp 5–7 Hoover ER, Middleton JN (1981) Laboratory evaluation of PDC drill bits under high-speed and high-wear conditions. (1949) “Rotary percussion drilling.” Drilling and Production Practice. (2014) “San Francisco Basin tight reservoir play: defining benefits of hammer bit/percussion drilling, onshore Brazil.” In IADC/SPE Drilling Conference and Exhibition. Gerlero, M., Soroldoni, T., and Barreto, D. (2005) “Rotary percussion sounding system for in situ rock mass characterization.” Alaska Rocks 2005, the 40th US Symposium on Rock Mechanics (USRMS).
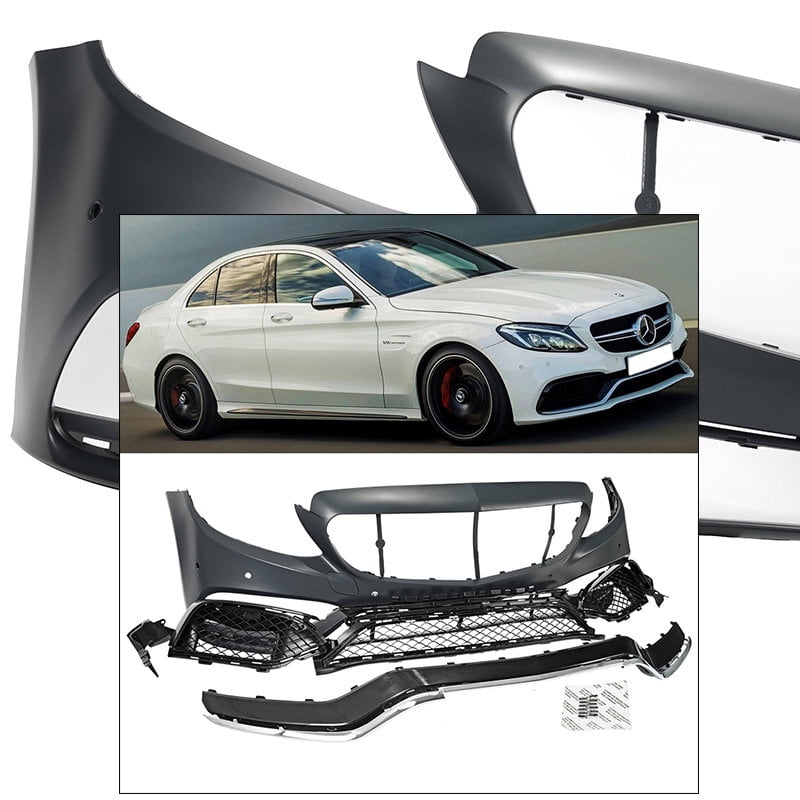
The results obtained in this paper can enhance the understanding of rotary percussive drilling technology and provide theoretical basis for the design of impactor.Ĭhitty, D. The field applications show that the use of high-frequency impactor can bring obvious ROP rising in the hard formation drilling. The results show that the hard rock is more prone to occur brittle failure under rotary percussive cutting, the rotary percussive drilling technology can improve the stress state of the PDC cutter, better to protect the cutter and improve the drilling efficiency the magnitude of impact amplitude should not be too large when it reaches the threshold to break rock, the impact frequency has significant influence on MSE rotary percussive drilling technology is not suitable for soft formations.
#PDC TO HARD ROCK PDC IN CAB CRACK#
The crack propagation, chip formation, damage evolution, mechanical specific energy (MSE), and other problems are discussed.

This paper established three-dimensional finite element model of rotary percussive cutting by single PDC cutter. However, the rock breaking and ROP rising (rate of penetration) mechanism are not clear enough to some extent. * Above is our ordinary ways of package and delivery.Rotary percussive drilling technology can solve the problems of low efficiency and high cost in deep hard formation drilling effectively it can improve drilling efficiency and reduce stick-slip vibration in order to improve transmission efficiency of WOB (weight of bit). PDC bit may be used with air, mud, or foam flushing. PDC bit has a long working life, very fast penetration and high percentage core recovery in soft to hard rock formations.īecause of the polycrystalline diamond cutters set on the crown, PDC bit has a long working life, very fast penetration and high percentage core recovery in soft to hard rock formations. Georbor S PCD Drill Bits for hard and medium hard rock PDC Core drill Bit Geothermal Drilling
